Process Simulations (Media Fill): What to Do When They Fail
Discover actionable steps for handling Media Fill simulation failures in pharmaceuticals, from root cause analysis to implementing corrective actions .
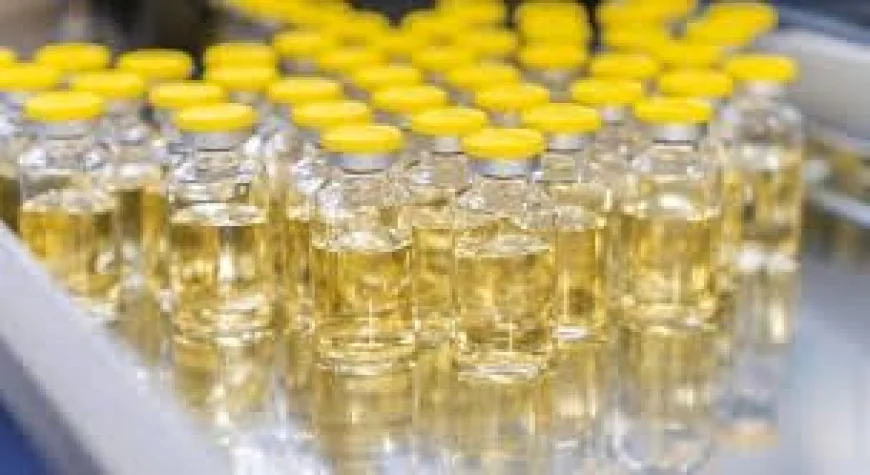
In the pharmaceutical and biotechnology industries, maintaining the sterility of products is paramount. One of the critical procedures to ensure this sterility is the Media Fill test, also known as Aseptic Process Simulation. This test simulates the entire aseptic manufacturing process using microbiological growth medium instead of actual product, to verify the effectiveness of the aseptic techniques and facilities. However, when these simulations fail, it can be a significant setback.
Understanding Media Fill Failure
A failure in a Media Fill test is indicated when microbial growth is observed in the growth medium after incubation. This signals a potential breach in the aseptic process, which could lead to contamination in actual production if not addressed.
Steps to Take Following a Failure
1. Immediate Investigation:
- Conduct a Root Cause Analysis: Assemble a team of experts to thoroughly investigate the failure. Use methodologies like the 5 Whys, Fishbone Diagram, or Failure Mode and Effects Analysis (FMEA) to identify the root cause.
- Review Documentation: Go through all related documentation, including SOPs (Standard Operating Procedures), batch records, and environmental monitoring data to trace the failure back to its origin.
2. Containment:
- Isolate Affected Batches: If any batches of product were produced during the time of the failed simulation, they should be quarantined for further investigation.
- Stop Production: Temporarily halt production in the affected area until the investigation and corrective actions are implemented.
3. Communication:
- Internal Communication: Inform all relevant stakeholders within the company, including quality assurance, production, and upper management, about the failure and the steps being taken.
- Regulatory Compliance: If necessary, report the failure to regulatory bodies like the FDA or EMA, as per compliance requirements. Transparency can mitigate potential regulatory issues.
4. Corrective and Preventive Actions (CAPA):
- Develop a CAPA Plan: Based on the root cause analysis, create a detailed CAPA plan. This might involve retraining personnel, revising SOPs, enhancing equipment maintenance, or upgrading facility design.
- Implementation: Execute the CAPA plan with precision, ensuring every team member understands their role.
5. Verification:
- Rerun Media Fill Test: After implementing corrective actions, conduct another Media Fill test to verify the effectiveness of the changes. This should be done under similar conditions to the failed test, with additional scrutiny.
- Monitor Results: Keep a close eye on the results from subsequent tests and environmental monitoring to ensure no recurrence of the issue.
6. Documentation and Review:
- Update Records: Document all findings, actions taken, and outcomes in a comprehensive report. This not only aids in future audits but also helps in refining processes.
- Continuous Improvement: Establish a routine review mechanism to prevent future failures. This could involve periodic training sessions, equipment audits, or updating protocols based on industry innovations.
What's Your Reaction?
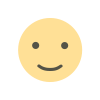
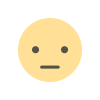
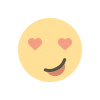
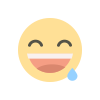
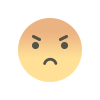
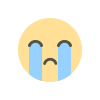
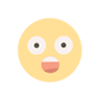