Understanding the Role of Isolators in the pharmaceutical industry
Discover the critical role of isolators in the pharmaceutical industry, enhancing product safety, ensuring contamination control, and maintaining sterile environments during drug manufacturing processes. Learn how isolators contribute to compliance with stringent industry standards and improve operational efficiency.
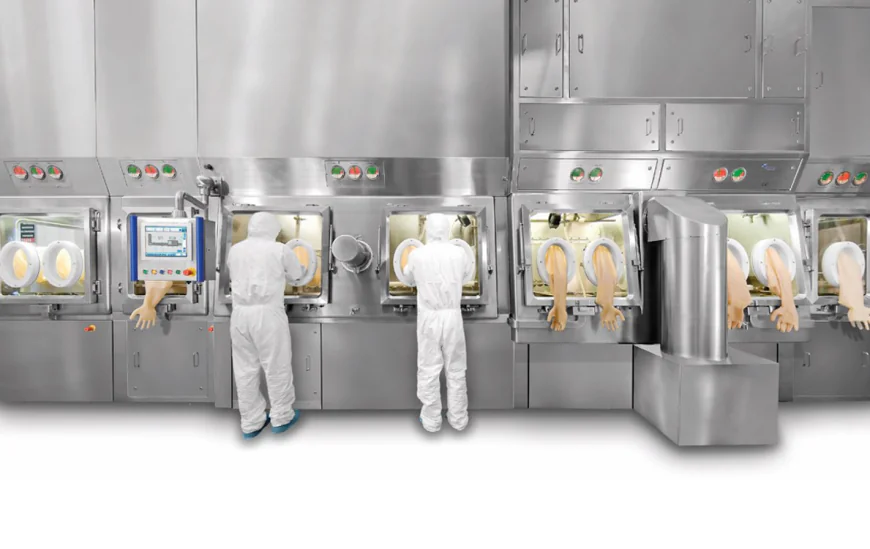
Pharmaceutical isolators are sophisticated containment systems designed to create a controlled and sterile environment. They play a crucial role in ensuring the safety and quality of pharmaceutical products, from the initial stages of drug development to the final production phases. By providing a physical barrier between the product and the external environment, they ensure stringent control over contamination risks and protect both the compounds being handled and the personnel involved.
Key Features and Components
1. Containment and Separation:
- Barrier Technology: Isolators are built using robust materials that form a secure barrier to isolate the internal environment from external influences. They effectively prevent contamination from external microorganisms, particles, and potential environmental pollutants.
2. Environmental Control:
- Pressure Control: Most isolators operate under negative pressure relative to the surrounding environment, which prevents contaminants from entering. Some systems might use positive pressure to protect the product from external airflows.
- Temperature and Humidity Regulation: Maintaining precise temperature and humidity levels is crucial for certain processes, especially those involving chemical reactions or the storage of sensitive materials.
3. Air Filtration Systems:
- High-Efficiency Filters: HEPA (High Efficiency Particulate Air) or ULPA (Ultra Low Penetration Air) filters are standard in isolators to ensure that the air inside remains free of microorganisms and particulate matter. These filters trap particles as small as 0.3 micrometers, providing maximum contamination control.
4. Operator Interface:
- Glove Ports: Operators interact with interior components via glove ports, which are airtight gloves integrated into the walls of the isolator. This setup allows manipulation and handling of materials without opening the system.
- Transfer Systems: Materials are typically transferred through specialized systems to maintain the sterile barrier, such as rapid transfer ports (RTPs) that allow quick exchange of items without contamination risks.
5. Validation and Compliance:
- Regulatory Standards: Isolators must meet stringent regulatory standards set by bodies like the FDA and EMA, ensuring that they are validated for their specific applications. Validation involves a comprehensive assessment of their ability to maintain sterile, controlled environments and ensure containment.
Applications in Pharmaceutical Processes
1. Aseptic Processing:
- Sterile Manufacturing: Isolators are integral to the production of sterile injectables and other critical pharmaceuticals. They ensure the aseptic processing of drugs by creating environmental separation during manufacturing.
2. Handling Cytotoxic and Hazardous Compounds:
- Safety in Research and Development: In laboratory settings, isolators protect researchers from exposure to toxic substances like chemotherapy drugs and biohazardous materials. This safety measure is vital for those working on potent compounds and leads to safer, more efficient workflow practices.
3. Biological Product Handling:
- Vaccine and Biologic Manufacturing: Biotechnology and the production of biologics involve sensitive processes that must be conducted in sterile environments to ensure product integrity and compliance with regulatory requirements.
4.Innovative Applications:
- Personalized Medicines: With the rise of personalized medicine, isolators play a critical role in small-scale, bespoke production processes, ensuring that every batch adheres to high-quality standards.
The Future of Pharmaceutical Isolators
As the pharmaceutical industry continues to evolve, the role of isolators may expand with the integration of advanced technologies. Emerging trends include the use of automation, improvements in material technology for better barrier performance, and the application of digital tools for monitoring and validation processes. These advancements highlight the ongoing commitment to enhancing the safety and efficiency of pharmaceutical manufacturing.
What's Your Reaction?
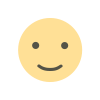
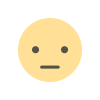
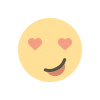
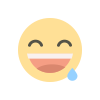
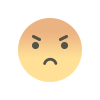
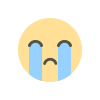
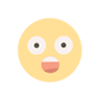